CRGM ring roller mill is mainly composed of machine body, machine base, crushing device, grading device, discharging system, transmission device and motor.
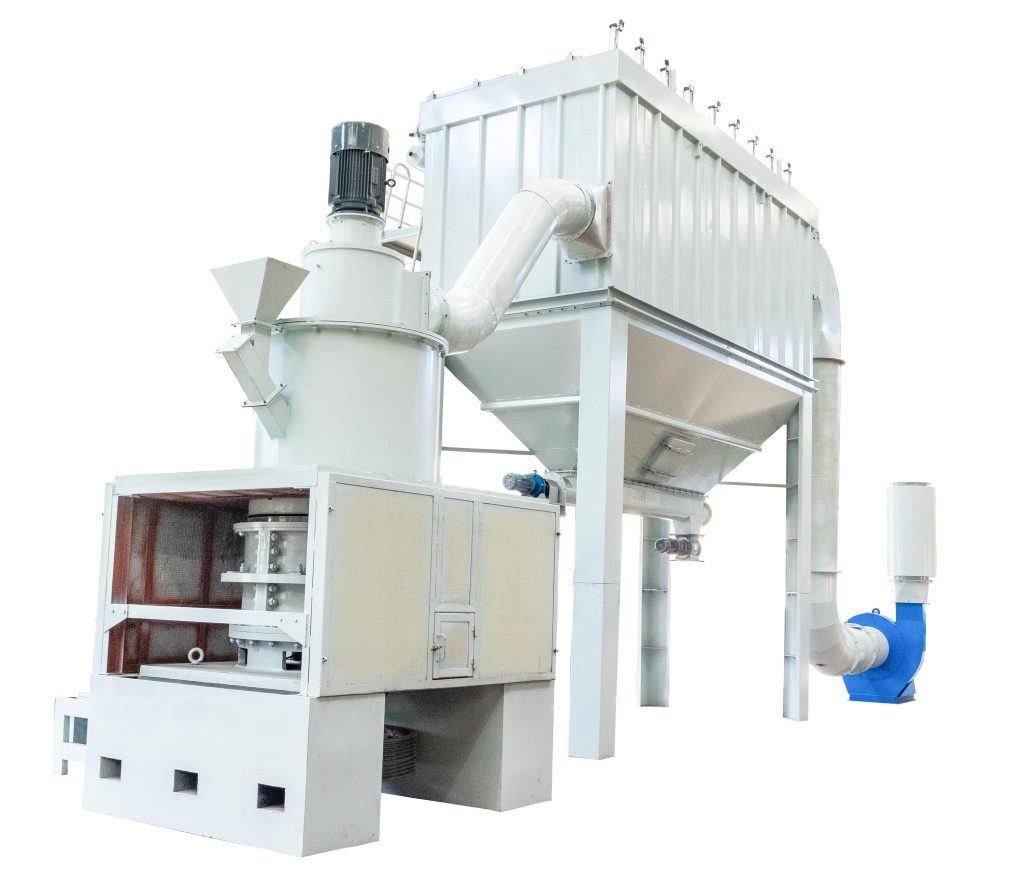
Working Principle
CRGM roller mill crushes materials by the principle of impact, extrusion and grinding. There is a large clearance between the grinding ring and the pin shaft installed on the grinding ring bracket. When the material passes through the gap between the grinding ring and the grinding ring, it is crushed by the impact, extrusion and grinding of the grinding ring.
The crushed material falls to the throwing plate under the action of gravity and is thrown into the air flow into the classification chamber for classification. The qualified fine powder enters the back-end collection system through the classification wheel, and the coarse material is thrown into the diversion ring to avoid and fall back into the crushing chamber for crushing. When the double-layer grinding ring crusher is working, the material is crushed again when it passes through the gap between the second layer of grinding ring and the grinding ring.
Application in non-metallic mineral industry
CRGM roller mill is mainly used for crushing minerals such as calcite, dolomite, limestone, marble, wollastonite, etc. Taking calcite as an example, the crushing process is mainly divided into four stages:、
Crushing of raw materials
Large pieces of calcite are crushed by the crusher to the feed fineness that can enter the CRGM mill (15mm - 50mm).
Grinding
The crushed small pieces of calcite are sent to the storage hopper by the elevator, and then sent to the grinding chamber of the CRGM mill for grinding evenly and quantitatively by the feeder.
Classification
The ground materials are classified by the CRGM classification system, and the unqualified powders are returned to the main machine for re-grinding after being classified by the CRGM classifier.
Finished product collection
The powders that meet the fineness are separated and collected by the air flow through the pipeline into the dust collector. The collected finished powders are sent to the finished product silo by the conveying device through the discharge port, and then packaged uniformly by a powder tank truck or an automatic packaging machine.
Product advantages of CRGM roller mill
High crushing ratio and high energy utilization rate. Particles with feed size <10mm can be processed into micro powders <10μm (under the standard of D97%) in one time, with high fine powder content and large specific surface area of the product. Good and stable product particle size. Built-in grading mechanism, unique grading wheel structure, good effect, and infinitely adjustable fineness as needed. Environmentally friendly and energy-saving. Production under negative pressure, less dust in the working environment; semi-automatic control and unique process are adopted to greatly improve production efficiency and reduce energy consumption. Low wear. Grinding wheel and grinding ring are made of special wear-resistant alloy steel or high chromium, and the service life is increased by 2~3 times.
Parameters of Superfine Grinding mill-Ring roller mill
mesh (D97) | CRGM1000X | CRGM2000X | CRGM3000X | ||||||
---|---|---|---|---|---|---|---|---|---|
capacity (kg/h) | power consumption (kW/h) | total power (power) | capacity (kg/h) | power consumption (kW/h) | total power (power) | capacity (kg/h) | power consumption (kW/h) | total power (power) | |
800 | 2500~2800 | 43 | 152kw | 4000~4500 | 40 | 237kw | 5500~7000 | 37~38 | 287~340kw |
1250 | 1500~1800 | 67 | 4000~4500 | 68 | 3500~4000 | 50~56 | |||
1500 | 1000~1300 | 92 | 4000~4500 | 92 | 2500~3000 | 67~70 | |||
2000 | 650~750 | 125 | 4000~4500 | 110 | 1500~2000 | 100~114 | |||
2500 | 600~650 | 135 | 4000~4500 | 119 | 1100~1500 | 134~153 | |||
3000 | / | / | / | / | 1000~1200 | 183~208 |